How an Industrial Boiler is Made?
An Industrial Boiler is a Magnificent Engineering Product. In This Post, We Will Learn, How an Industrial Boiler is Made.
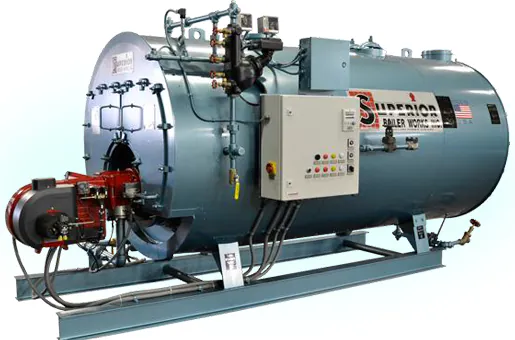
A boiler is used to heat water and generate steam from water. Steam is used in food processing plants to power plants. In power plants, steam is used to run a steam turbine to generate electricity. Steam has an effective role in our modern life.
Generally, there are two types of boilers available. The first one is a water tube boiler and the second one is a fire tube boiler. Between these two types, you will find more categories. In this post, we will learn about “How an Industrial Boiler is Made?”
Industrial Boiler, How it’s Made:
The water inside the boiler is heated by Oil, Natural GAS, or Electricity. That means inside the boiler, there is lots of pressure. The making of an industrial boiler starts with the plasma torch. This torch cut the holes in a solid sheet of special steel. However, the thickness of the steel sheet depends on the pressure inside the boiler that needs to be handled. If it needs a high-pressure large amount of steam then the thickness of the steel sheet will increase.
Then a worker bends this steel sheet with a hydraulic press. The steel sheet will become the inner shell of the boiler. This inner shell will be used to heat the water and generate steam. But remember worker was pressing a flat steel sheet to make it round inner shell. That means this steel sheet needs to join two sides together to make a complete round boiler inner shell. For this reason, a worker makes an edge at both sides of a steel sheet with a grinding machine for welding.
When the boiler's inner shell comes to its final shape then it is time for welding. Workers use a submerged arc welding machine and deposit a special material during the welding operation. This special material granular protects the welding from any air contamination. When welding is finished the worker removes the special material granular. In this way, we can get perfect welding.
In the next step, the worker welds the boiler head or tube head inside the boiler shell by manual hand welding. Then they fit the steel pipe inside the boiler head from one end to another end. After inserting all steel pipe workers secure all pipe by welding. Next, a combustion chamber is inserted into the remaining space of the inner shell. Then they test this fully assembled pressure vassal with water and check for any leakage. However, these tests were only performed between the combustion chamber and the boiler shell. Because inside the combustion chamber, a burner will fitted into the combustion chamber.
Next, some insulation material will be warped with the pressure vassal. This insulation material helps to retain heat. Then they warp the outer jacket around the shell and secure it in place with some sheet metal screws. After that, a blower is installed with a pressure vassal. This blower will supply the fresh air into the combustion chamber. Next worker attached a water column to the outer shell of the boiler. This water column provides some safety inspection like water level during operation. It also has some sensor that provides valuable data to the boiler operator.
Now come to the electrical control section. A worker installs an electrical control device that helps to operate this boiler automatically. Then they power up the boiler by firing the burner. After that, they open the steam outlet pipe and on a test line and check whether all control devices are working or not. This test includes water level and blower testing. When the boiler generates the correct amount of heat and steam then it passes the test. Then manufacturer labeling with each unit of boiler before it comes to you.